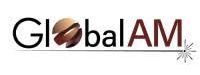
The GlobalAM project aims to overcome the limitations of Laser Powder Bed Fusion (LPBF) in producing complex geometries at a large scale by developing a hybrid production approach that combines the flexibility of LPBF with conventional manufacturing methods.
Project Description
Additive manufacturing (AM) has emerged as a transformative technology, offering high efficiency, cost-effectiveness, and adaptability. However, despite the advancements in laser powder bed fusion (LPBF), AM faces significant challenges in producing complex geometries cost-efficiently at a large scale. The EU-funded GlobalAM project aims to overcome these barriers by developing a hybrid production approach that combines the flexibility of LPBF with conventionally manufactured substrates. This innovative methodology is designed to accelerate the production process significantly, particularly for small component volumes. Additionally, the project will integrate advanced technologies and methodologies to enable large-scale manufacturing, as demonstrated by the production of a cooling device for power electronics.
Objective
While LPBF inherently facilitates the creation of complex geometries, it has yet to penetrate mass markets due to lengthy cycle times and challenges related to product precision and quality. The GlobalAM project addresses these limitations through a hybrid production approach, where complex components are constructed using LPBF on near-net-shape geometries of conventionally manufactured substrates. This approach offers the potential to dramatically reduce production times and costs.
GlobalAM will advance and combine state-of-the-art technologies, including:
- Beam shaping and beam splitting to optimise laser utilisation.
- In-situ geometry correction to ensure precision.
- Process monitoring and control to enhance production reliability.
The project’s advanced machine concept will enable the fixation of multiple substrates and precise laser beam positioning to support large-scale manufacturing.
As a demonstrator, the project will develop a cooling device for power electronics, chosen for its prototypical representation of typical challenges:
- Fabrication of complex metal geometries from materials such as copper.
- Integration with ceramic-based substrates requiring micrometre-scale precision.
By addressing these technological challenges, GlobalAM aims to unlock the potential of LPBF for large-scale applications, particularly in the multi-billion-euro market of power electronics. The project's outcomes promise significant technological, economic, and environmental benefits, including reduced production times, improved material utilisation, and lower costs.
To achieve its ambitious objectives, the GlobalAM consortium brings together experts from leading universities and globally renowned companies specialising in production technology, laser systems, process development, monitoring and control, modelling, and advanced multi-material powder production. This multinational collaboration ensures a comprehensive and innovative approach to advancing AM capabilities.